
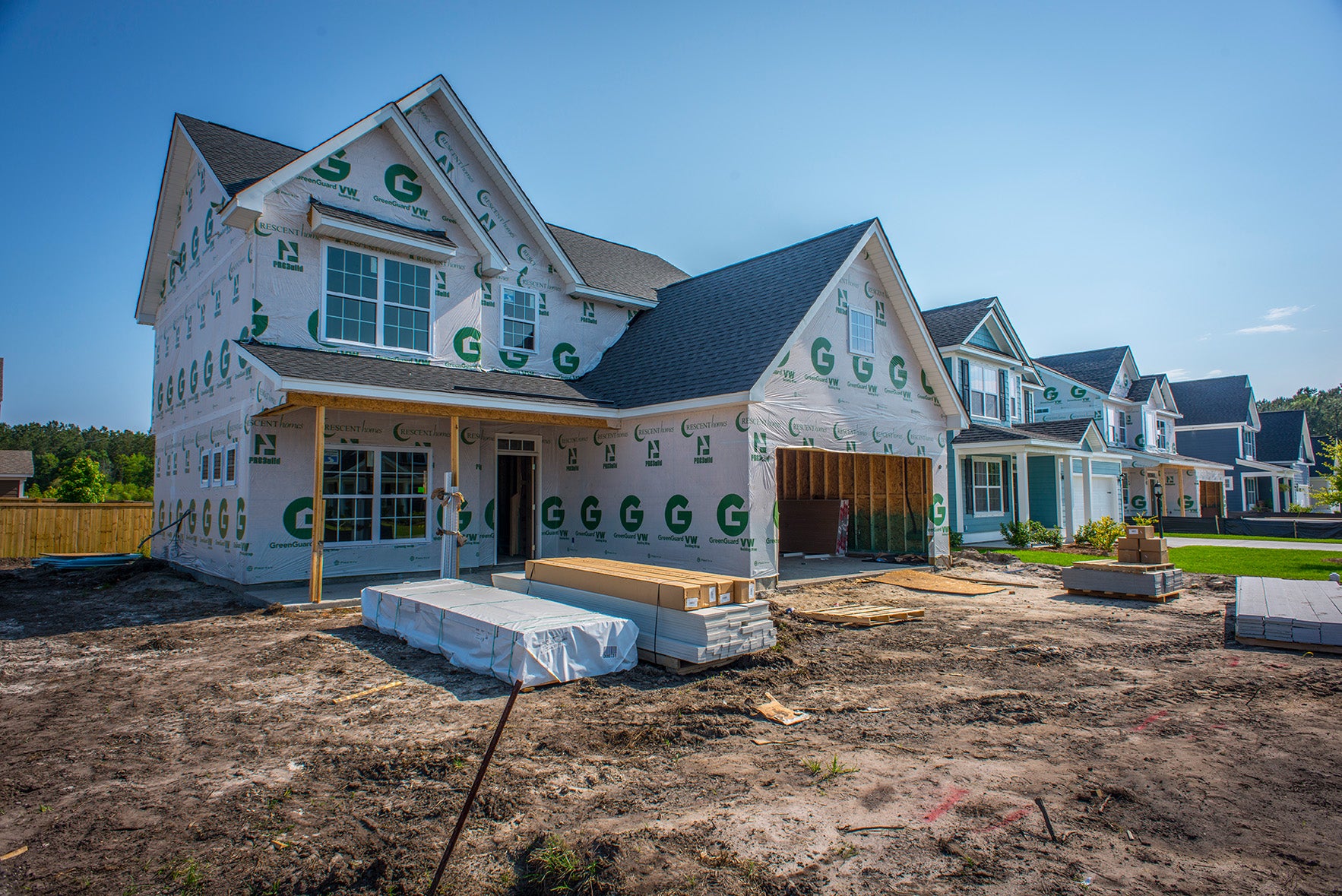
And because it is noncombustible, it will not burn or give off toxic fumes.

Cured blocks or panels of autoclaved aerated concrete are joined with thin bed mortar. In the factory where it is made, the material is molded and cut into precisely dimensioned units. In fact, this type of concrete contains 80 percent air. Check and see if the property needs re-platting, which is a long process involving many county departments.Autoclaved aerated concrete (AAC) is made with fine aggregates, cement, and an expansion agent that causes the fresh mixture to rise like bread dough.
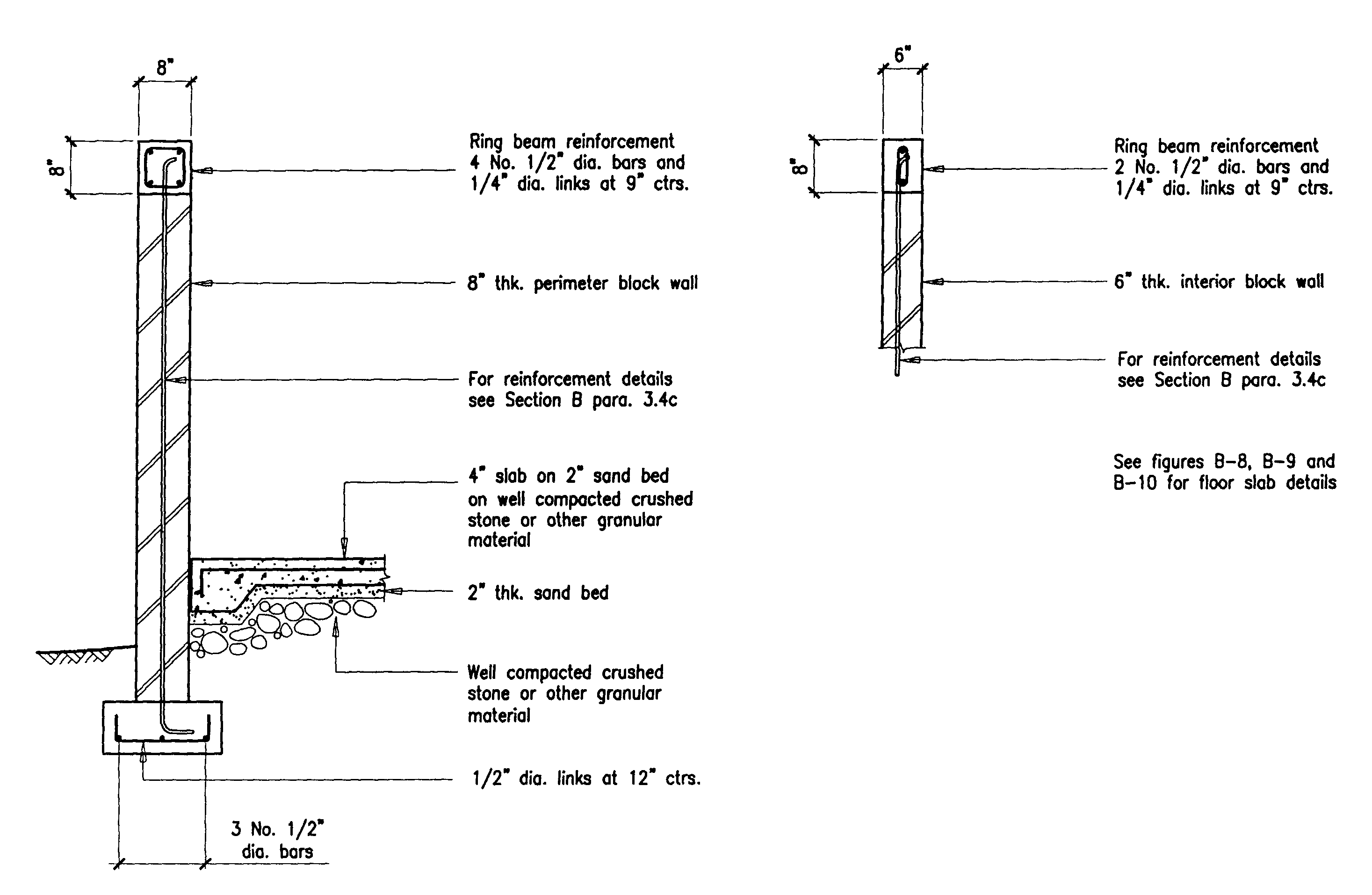
Hire a surveyor to produce a boundary survey and an elevation certificate for the property, and make sure that the survey shows all easements.Conduct environmental testing to determine if there is any contamination in the soil.Hire a soil engineer to determine if the building requires piles at the location.Verify that the water and sewer lines can handle the needs of the business.Does the area have sufficient fire hydrants and flow to handle a fire emergency at the location?.Ensure that the nearby infrastructure can handle the needs of the future business.
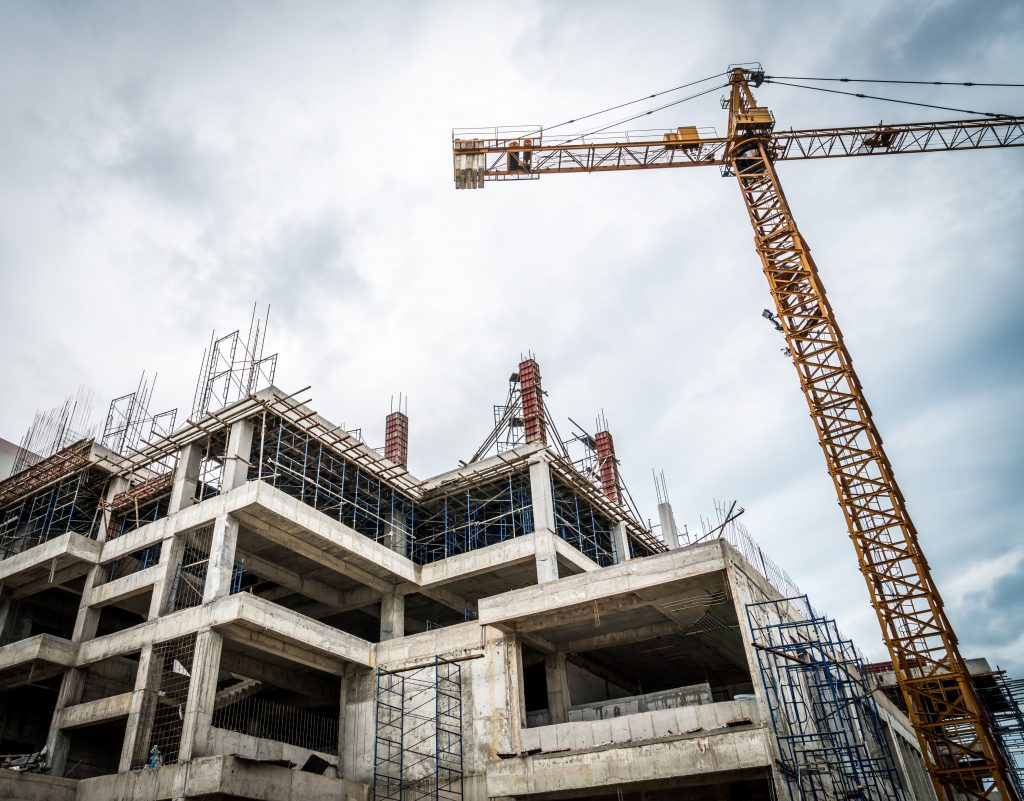
Ensure the location does not have a moratorium on building.Verify appropriate zoning for the location of the new construction.The location for commercial construction must consider access to clients and employees and proximity to other buildings.A developer must consider these ten factors before choosing a location for a new commercial building: A developer's selection of the location for a new commercial building is one of the first and most important decisions he or she makes for the project.
